The Covenant School switches to VRF
The Covenant School is a co-educational day school in Charlottesville, Va teaching children from Pre-K to high school seniors. The school has offered a unique learning culture, blending education with non-denominational Christian principles for almost 40 years. They were the first Christian school in the state to be accredited by the Virginia Association of Independent Schools and have grown tremendously, adding a second campus for their now 700 students.
As they invested in expansion and remodels to keep The Covenant School a premier destination for students, renovations to aging HVAC equipment and their systems were next in line. The school was experiencing terrible humidity issues and decided it was time to replace their outdated pneumatic two-pipe system with a Variable Refrigerant Flow structure. VRF systems are made up of outdoor units which connect to multiple indoor units through refrigerant piping. This allows both heating and cooling to be tailored to individual zones throughout the building.
The kicker was it had to be completed within 60 days during summer break while the students were away. A summer with a hard end date is a summer that flies by on the calendar! In a time where every single person in every single industry is somehow affected by supply chain delays, Southern Air’s tradespeople showed up to school with the answers, not excuses.
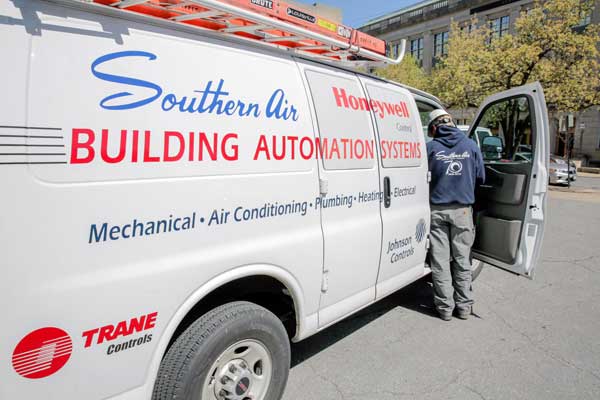
Southern Air’s Service department has developed great relationships at The Covenant School. For more than 20 years, our service teams have maintained their chillers, boilers and other heating and cooling equipment keeping class in session. When they recognized the need for a major renovation, it was only natural for The Covenant School Facilities Director Bob Michie to reach out to Ray Spivey, Southern Air Service Charlottesville Branch Manager for guidance. Spivey connected Michie to Doug Davidson, Southern Air Vice President, our engineering group, and our mechanical and electrical designers who came up with a plan.
The school chose to resolve their humidity issues by switching from a pneumatic system consisting of unconditioned make up air units and individual fan coil units to a VRF system. The design/build project was handed over to Southern Air’s engineering department who expertly created the schematics of how the system would be laid out. Steve Mullen consulted with the customer to understand their specific needs and goals before working with Jarrett Rusher on the mechanical design and Alan Cleveland on the electrical design. Their drawings resulted in our construction teams installing four Samsung VRF systems consisting of 58 indoor units, six outdoor units, and two dedicated outdoor air systems.
The electrical scope involved wiring all the new equipment associated with new VRF system. We added two new electrical panels, which supply the current equipment and provide the capability to supply future expansions to the system. Cleveland worked closely with Keith Bourne, Southern Air Electrical project manager to design a system, using equipment we could actually receive in time due to supply chain issues. This is where our teams in the Prefabrication Shop offered innovative solutions to our supply chain issues. They offered tremendous expertise with designing and fabricating connection assemblies for different equipment making it possible to connect each piece in a fraction of the time normally required.
Southern Air Richmond’s Mechanical construction teams started the first 10 days of the job in full demolition mode! Led by mechanical project manager Cliff Myers, step one was getting the old, large, clunky fan coil units out of the building. This involved cutting many of them in half to get them down from the top floor! Southern Air’s Richmond teams installed the new units and its duct work (made in our fabrication shop), our plumbing mechanics put in condensate drain piping, and our commissioning team ran refrigerant piping and conducted the equipment start-ups.
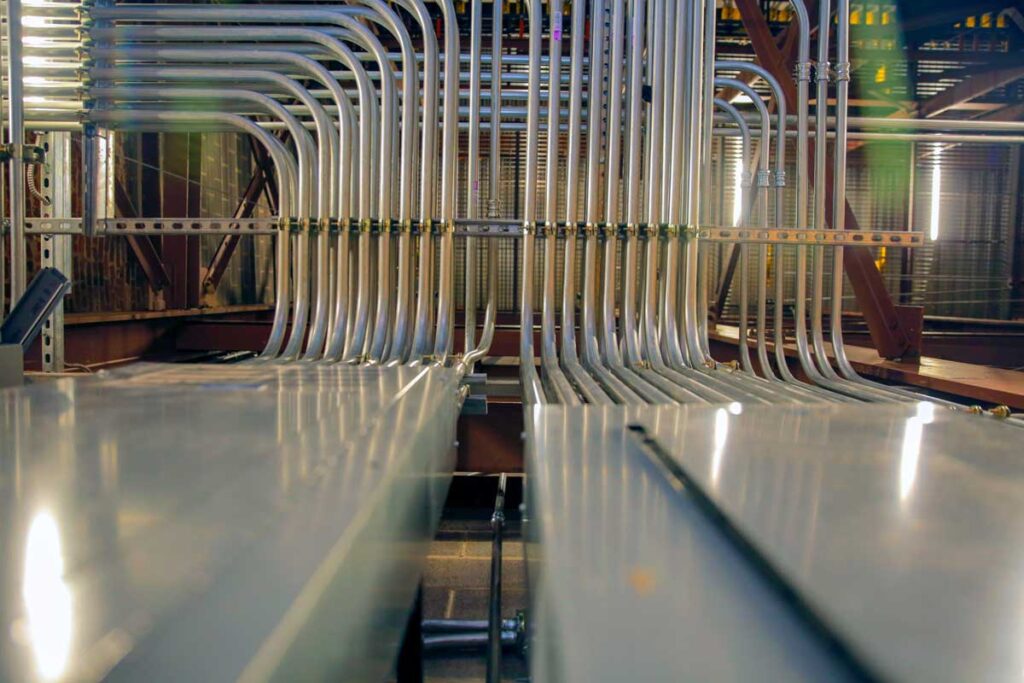
Much of the challenge came from the large amount of equipment and refrigerant piping to be installed in such a short amount of time. Our teams endured six and seven day work weeks, many times in tough conditions. Running refrigerant piping on the school’s white rubber rooftop in the sweltering summer heat is not the most desired task but for John Weedon, Southern Air Commissioning foreman and his team; it was no sweat! They installed 7,650 feet of refrigerant piping and 4,900 feet of soft copper from the mode control units to the individual indoor units.
“Most of the building automation work doesn’t begin until the equipment is up and running,” says Garret Ogden, Building Automation Solutions Manager. “The schedule on this project left little to no flexibility, so while everyone had to do their part for this project to be successful the commissioning crew is deserving of a big shout out for getting us to the finish line on time.”
Jeff Claytor, Southern Air B.A.S. project manager led the installation of the school’s new direct digital controls. His team put in a Honeywell control system providing a user-friendly interface for the school to control and monitor their new equipment. This will provide much more flexibility in temperature control compared to the dated pneumatic two-pipe system we removed.
Southern Air’s Electricians were able to get ahead of schedule during spring break when they installed two electrical feeders (400-amp and 225-amp) in student areas not accessible during school hours. We had concerns about running 600 feet of hard pipe over acoustic ceiling tiles and ultimately chose to use a pre-assembled flexible feeder cable.
“I was not sure this was a solution that would work but was convinced to try it by Steve Kozella and Hosteen Vest (Southern Air Electrical Foremen) who badgered me until I gave in,” says Bourne. “We realized a significant savings in labor and material costs by using this method. I was wrong about that cable solution and I think the guys enjoy reminding me of that fact! The team did tremendous work.”
The Covenant School is a great customer to Southern Air and one we’ve cared about for many years. At the end of the day, the work we are doing, the work we have done and the work we’re planning is for children and their teachers to be comfortable in their school as they learn. The many Southern Air departments who helped with this job are nothing less than impressive.
“I would like to express my gratitude for the work performed by Southern Air these past couple of months,” says Greg Porter, Covenant School Facilities Director. “Not only did Southern Air meet the desired timeline, the work was performed in a truly professional manner. I have spoken with many of our school employees who interacted with Southern Air’s workers and they all were extremely impressed with the courteous nature exhibited on a daily basis. We have enjoyed working with Southern Air over the years and this latest project reinforces the reasons why.”